Titanium has good biocompatibility, so it is selected as the most ideal implant product for human body. Over the past ten years, many scientific research departments, medical schools and hospitals in the world and China have also done a lot of basic and clinical research. In depth and breadth, titanium has been recognized as the most ideal implant product for human body. In these years, artificial femoral head, wrist joint, knee joint, cultivated teeth and skull repair have been done with titanium. There are thousands of records of pacemaker and so on. Titanium is the most ideal product for human implants in the reports so far. The design of orthodontic devices needs to conform to the complex shape of bones and joints, so the processing of these parts is also complicated. These devices processed from titanium bars need to cut off a large number of materials, so the process is very expensive because of the low cutting performance index of many materials. Therefore, some parts are cast to the final shape of the parts, which often requires complex and expensive fixtures.
Titanium 6AL-4V ELI is a standard product for making hip joint, bone screw, knee joint, plate bone or organ, denture and surgical equipment. However, cobalt-chromium alloys are used more and more frequently because of their strong, tighter particle size and cleaner than titanium. The cutting force required to process titanium alloys is only slightly greater than that required to process steel, but the metallurgical properties of titanium alloys make it more difficult to process than steels with appropriate hardness. Titanium has a work hardening property, which eliminates the binding metal (crimping) in front of the cutting tool. This helps to increase the shear angle in processing, thus forming a thin chip, which is touched on a suitable small area with the appearance of the cutting tool. Because of the work hardening, the feed can not be stopped in the moving touch between the tool and the workpiece. In this way, the large supporting force occurring in the processing, combined with the friction force produced by chips in the touch area, results in a large increase of heat in part of the tool area. The heat generated by cutting titanium will not be lost quickly because it is a bad conductor. Therefore, most of the heat is concentrated on the cutting edge and tool surface. Large bearing capacity and heat constitute crescent depression near the cutting edge, resulting in tool agility damage. To make matters worse, titanium alloys have a strong tendency to melt into alloys or revive chemical changes with the products in the tool at the working temperature. Another trend is that when chips are bonded to the cutting edge of the tool, the appearance of the tool is damaged. When the tool begins to damage, these difficulties will be doubled. Therefore, the tool used to process titanium and its alloys should be carefully monitored to ensure that the blade is sharp and replaced before blunting. The experience of processing titanium and titanium alloys is that if any change is seen in the process of processing, the tool should be changed immediately, because the change means that the tool will become blunt. Another reason for sticking to tool sharpness is that titanium can cause fire when cutting with damaged or damaged tools. When burned, oxygen occurs in the metal, so the fire will spontaneously ignite. Therefore, many titanium processing workshops do not report fire, they are equipped with life-saving system on machine tools.
Titanium has a relatively low elastic modulus and is more elastic than steel, so it tends to violate cutting tools in processing unless it is machined robustly or used as appropriate support. Slender parts tend to deflect under tool pressure, resulting in knife tremor, tool friction and errors. Through the processing experience, it is considered that the rigidity of the tool system is very important, and the sharp and accurate shape of the tool should be used. As a result of these pressures, new technologies are introduced to help manufacturers of medical parts to cope with competition and to produce these complex parts with high precision. Many innovations in EDM make the production of high-quality parts faster and eliminate many inherent problems in old processing technology.
Titanium, as a new product, has been developed and used in the pharmaceutical industry, medical devices and human implants in China for only 20 years. However, it has achieved great success and achieved remarkable social and economic benefits.
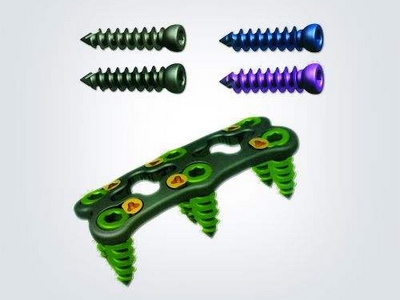
