How to make titanium springs?
- Why Choose titanium springs?
At present, there are two kinds of titanium alloy for spring, one is low-cost titanium alloy grade 5, the other is high-cost titanium alloy grade 19 (also known as beta-c or ti38644). They have low density (Grade 5 titanium alloy density 4.51g/cm3, grade 19 titanium alloy density 4.82g/cm3), high strength, corrosion resistance, and low shear modulus. Because of these excellent characteristics of titanium alloy, compared with steel spring of the same specification, titanium spring can be designed with smaller volume, lighter weight, longer life and better elasticity. So titanium spring is very popular among cycling enthusiasts, especially in cycling competitions, mountain bike downhill and other sports.
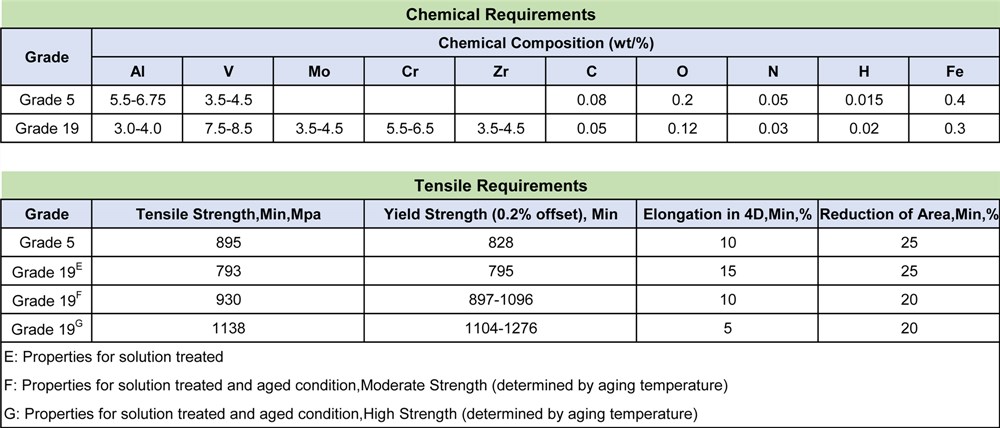
- Disadvantages of titanium springs
Although titanium spring has many incomparable advantages over steel, it also has its own disadvantages. The main disadvantage is that the cost is too high and many customers can’t accept it. There are many reasons for the high cost, including the following:
—Titanium is much more expensive than steel
—Titanium spring has more specifications and less quantity of single specifications, which leads to more material sizes, less quantity and high material cost
—The coiling process of spring is difficult and the yield is low
—Less single production batch
However, with the continuous maturity of production technology, the production cost of titanium spring continues to reduce, and customers will slowly accept the price of titanium spring.
- Production process of titanium spring for bicycle rear shock absorption
1) Spring design
According to the specification, model, color and material requirements of the shock absorber provided by the customer, the reasonable wire diameter, turns and free height of the spring are designed. According to the actual situation of raw materials, work out the production plan and construction period.
2) Production of raw materials
The reality of the titanium spring market is that there are many kinds and relatively few quantities, so in order to ensure the accuracy of each dimension of the spring, the titanium bars used in the spring are often of unusual dimensions, such as the diameter of 10.2mm, 10.7mm, etc., while the number of titanium bars with a single diameter is relatively small, which causes great trouble for us to make spring materials, and each link needs constant adjustment of the machine and production efficiency Low cost.
The material of bicycle rear shock absorption spring is generally titanium bar, and the key steps of making titanium bar for spring are heat treatment, grinding, polishing and flaw detection.
Heat treatment: the material heat treatment is generally solution or solution plus aging treatment, to ensure the strength and hardness of the material to be high, so as to ensure the high performance of the spring.
Grinding: the grinding process is to control the diameter tolerance of the material, so as to ensure the accuracy of the spring.
Polishing: the surface finish of the material has a great influence on the yield of the spring coiling process. Titanium bars with poor finish or surface defects are easy to break when the titanium spring is on coiling.
Ultrasonic flaw detection: all titanium bars for titanium spring must be subject to ultrasonic flaw detection, and can be produced only after confirming that there is no defect inside, so as to avoid fracture during coiling or actual riding.
In addition to process control, raw material selection often plays a decisive role. For example, the performance of titanium spring made of medical titanium alloy grade 5 and industrial titanium alloy grade 5 is different. Because the composition content of medical titanium alloy GR5 and industrial standard GR5 is slightly different, and the material performance is different, so choosing the appropriate titanium alloy has a great influence on the performance of titanium springs.
3) Titanium spring Coiling
Because we choose titanium straight bar instead of titanium coiled wire for spring production, we can only choose lathe and axis for titanium spring coiling. The experienced master should control the speed, pitch and turns of the spring to ensure that each spring is a high-precision titanium spring.
All springs are cold coiled, not hot coiled.
Check the surface of the coil spring for cracks. If cracks are found, the spring will be discarded.
Cut off the redundant material head at both ends of the spring, and pay attention not to touch the second circle when cutting.
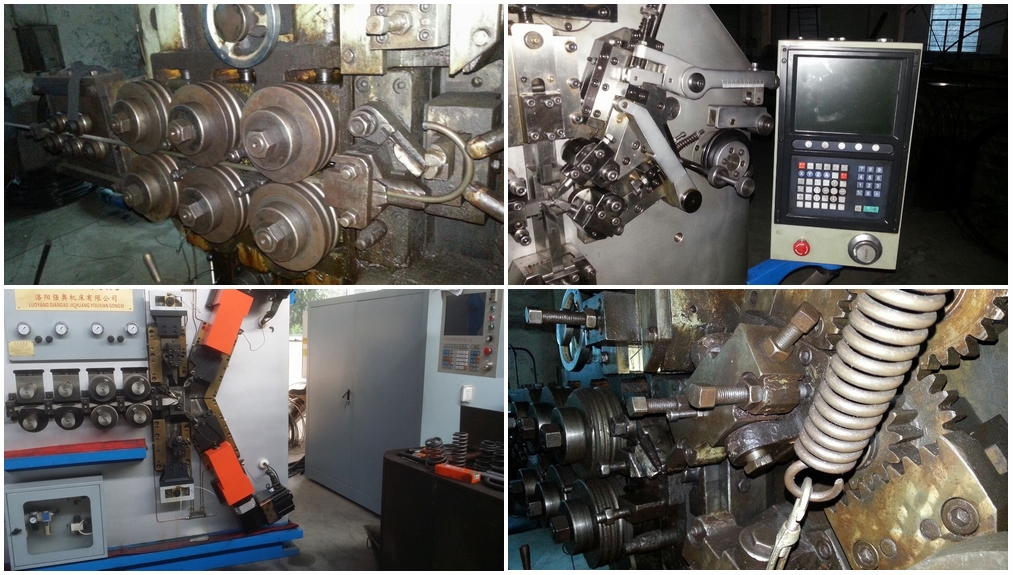
4) Spring Two Ends Flat Grinding
The rear shock absorption titanium springs of bicycles are all ground parallel, which is often another key technology. As mentioned earlier, titanium springs have many specifications and few quantities. When choosing automatic grinding machine, titanium springs of the same size must be ground together. Therefore, titanium springs must be ground manually, and the flatness of manual grinding cannot reach the flatness of automatic grinding machine. Therefore, it is necessary to carry out continuous manual correction and improve the flatness of spring grinding.
5) Heat Treatment
The heat treatment of titanium spring is generally solution treatment plus aging treatment. Solution plus aging can make the strength and hardness of titanium spring reach a very high level, and ensure that titanium spring has a very high performance. Due to the memory of titanium, titanium spring will generate some deformation after heat treatment, such as size change, verticality change and so on. Therefore, subsequent manual correction must be carried out.
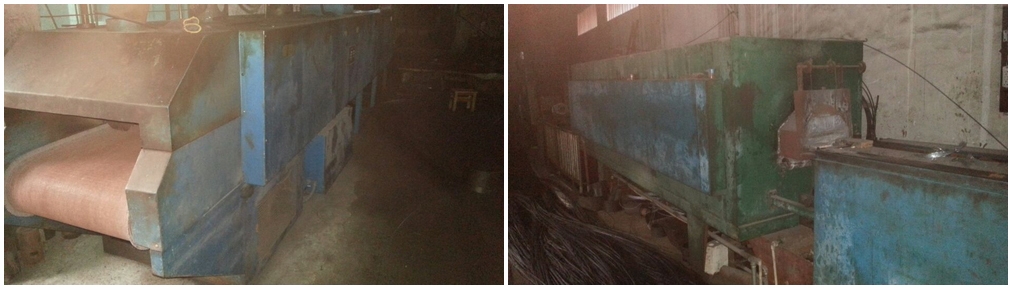
6) Detection
After production, titanium spring must go through further processing and testing, including strong pressure processing, stiffness testing, stroke testing, fatigue life testing, etc., to ensure that the spring meets the requirements of customers.
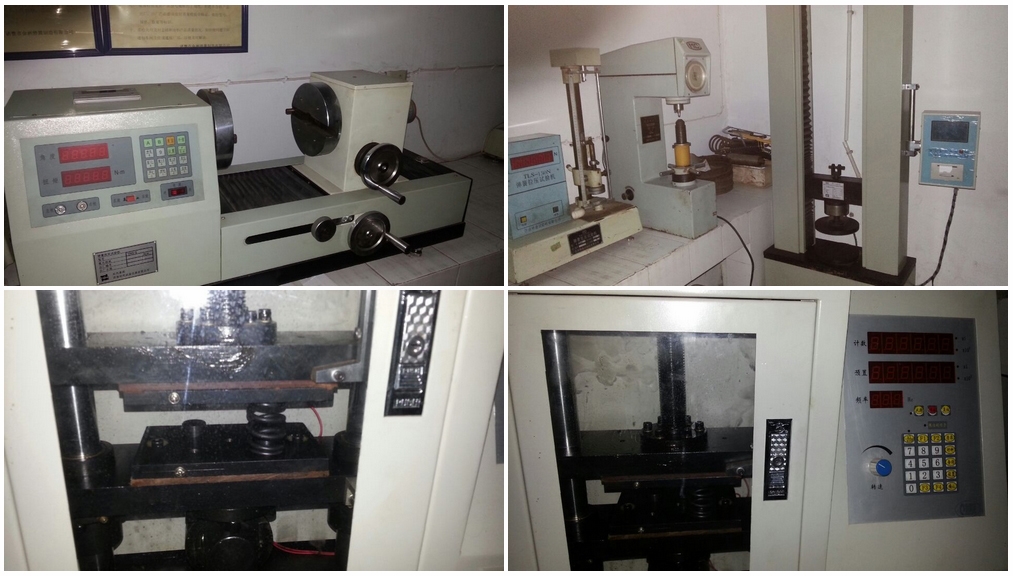
7) Manual correction & dimensional inspection
After heat treatment, the size of the spring will change slightly, which must be corrected manually to ensure that the spring can meet the requirements of customers. In the process of manual correction, constantly check the size of the spring, and correct the unqualified spring again until the size is qualified.
8) Shot peening
Shot peening is a necessary surface treatment process for titanium spring. Shot peening can not only remove burrs and beautify the appearance, but also improve the surface hardness and further improve the performance of titanium spring.
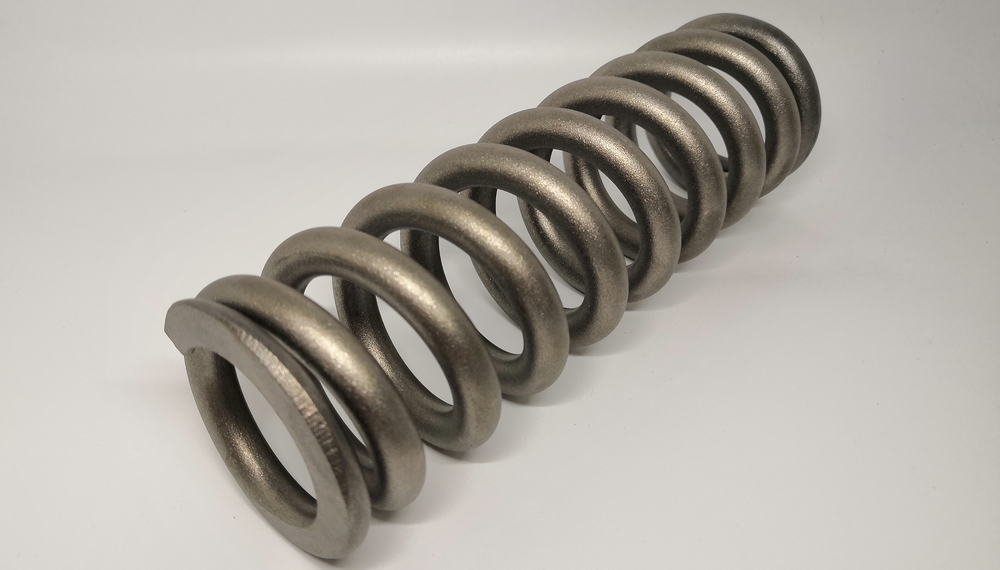
9) Coloring for titanium springs
According to the requirements of different customers for titanium spring color, titanium spring can go through the following processes to make various colors
Anodizing: gold, blue, purple, green, black, rainbow
Vacuum coating or nitriding: gold, black,Oilslick and burnt color.
Red color by special coloring process.
10) Logo Eteching
We provide free logo and specification engraving services, according to the content of customer requirements, using laser marking method to carve the surface of titanium spring.
11) Packaging
Choose bubble paper or pearl cotton to wrap each spring to ensure that the surface of the spring will not be damaged during transportation.