The main methods used in titanium alloy forging are free forging, open die forging (with hairy edge forging), closed die forging (without hairy edge forging), extrusion die forging, multi-direction die forging, partial die forging and isothermal die forging.
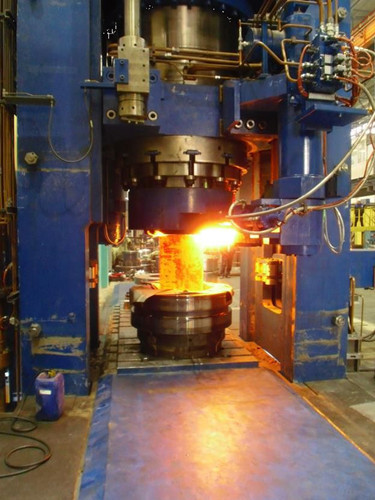
- Free forging
Free forging is usually carried out between two flat dies or dies without cavity. Free forging tools are simple in shape, flexible, short in manufacturing cycle and low in cost. However, the workload is high, the operation is difficult, the productivity is low, the quality of forgings is not high, and the processing margin is large. Therefore, it is only suitable for the case that there is no special requirement for the performance of the parts and the number of parts is small. For large forgings, free forging is mainly used as a blank-making process. In the free forging process, the billet can be forged into step bar, or the billet can be made into simple shapes such as round cake and rectangle by pier thickness or flattening.
- Open die forging (die forging with burr edge)
The billet deforms between two die-carved modules, and the forging is confined to the inside of the die cavity. The excess metal flows out of the narrow gap between the two dies, forming a rough edge around the forging. Under the action of the resistance of the die and the surrounding wool edge, the metal is forced to press into the shape of the die cavity.
- Closed die forging (no burr edge die forging)
In the process of closed die forging, no transverse edge is formed perpendicular to the direction of die movement. The die cavity of the closed forging die has two functions: one is used to shape the blank, the other is used to guide it.
- Extrusion Die Forging
There are two kinds of die forging: forward extrusion die forging and reverse extrusion die forging. Extrusion die forging can produce various hollow and solid parts. Forgings with high geometric accuracy and denser internal structure can be obtained.
- Multidirectional Die Forging
It is carried out on a multi-direction die forging machine. In addition to the vertical punching plug, there are two horizontal plungers in the multi-direction die forging machine. Its ejector can also be used for punching. The pressure of the ejector of the multi-direction die forging machine is higher than that of the common hydraulic press. In multi-direction die forging, the slider acts alternately and jointly on the workpiece from the vertical and horizontal directions, and uses one or more punches to make the metal flow outward from the center of the die cavity to achieve the purpose of filling the die cavity. There is no special forging edge on the parting line of the barrel.
- Partial die forging
In order to forge large integral forgings on existing hydraulic pressures, subsection die forging and cushion plate die forging can be used. The characteristic of parting method is that the forgings are processed step by step, one part is processed at a time, so the required tonnage of equipment can be very small. Generally speaking, this method can be used to process large forgings on medium-sized hydraulic presses.
- Isothermal die forging
Before forging, the die is heated to the forging temperature of the blank, and the temperature of the die and the blank is the same during the whole forging process, so that the large deformation can be obtained under the action of small deformation force. Isothermal die forging and isothermal superplastic die forging are very similar, but the difference is that the blank of the latter needs to be superplastic treated before die forging, so that it has fine equiaxed grains.