- Application of Titanium Alloy in Automobile
Titanium alloy automotive parts mainly include: turbine charger rotor blades made of TiAL, connecting rods and valves made of Ti-6AL-4V alloy, etc. In order to achieve low cost, Ti-6AL-4Sn-4Zr-1Nb-1Mo-0.2Si-0.3C alloy matrix prepared by powder metallurgy method was added with TiB particles dispersed Ti-based MMC, and engine valves were manufactured with the TiB particles dispersed in Ti-6AL-4Sn-4Zr-1Nb-1Mo-0.2Si-0.3C alloy matrix. This is an early application example of the development of new titanium-based materials for automotive engine valves. In addition to connecting rods and engine valves, the original secondary cost beta titanium alloy TImetaL LCB suspension spring is also the initial application example. Recent advances have been made in the development of Low-cost Titanium Alloys for engine valve and exhaust. Especially the demand of titanium alloy on exhaust system (muffler) of motorcycle is increasing, so the development of low cost alloy for exhaust system is more prevalent.
- Research Status of Titanium and Titanium Bar Alloys for Automobile
The countries that use most titanium in automobiles are the United States and Japan. First of all, the United States attaches great importance to the application of titanium in automobiles, such as Timet set up a special automobile factory to develop titanium automobile parts. The United States has produced titanium intake valves, exhaust valves, valve guards and connecting rods for racing cars. In Japan, titanium was used in racing cars and some sports cars as early as 20 years ago, but it has not been used in general passenger cars that pay attention to cost. For example, Nissan R382 won the Japanese competition because of its titanium alloy valve. At present, Titanium and its alloys are mainly used in automobiles, such as engine components, springs, poles, connecting rods, standard parts, wheels, power valves, etc. China is vigorously developing the promotion of automotive titanium. Firstly, the knowledge of titanium application is popularized to every corner of society through websites, newspapers, magazines and promotional meetings.
- Low Cost Technology of Titanium for Automobile
Titanium is much more expensive than aluminium and steel because of the cost of smelting and processing. Melting cost is essentially the energy cost necessary to separate titanium from oxygen. Processing cost generally refers to the processing cost and polishing cost at lower temperatures. The most noticeable technology is near net-shape permanent casting and powder metallurgy (P/M method). Considering the cost, P/M method should be adopted. A precedent for the use of P/M titanium components in cars is the valves on Toyota’s Alteezza. Ti-6Al-4V automobile parts with sufficient strength can be obtained by pressing/sintering low-cost metal powder mixture. In this case, there is no need to carry out HIP (hot hydrostatic compression forming) and other redundant compression processes, and the cost will not rise. At the same time, TiB2 or TiC alloys with improved rigidity and wear resistance were developed. In the TiC alloy market, the powder cost is $4/kg ($1.80/1b). Metal matrix composites (MMC) based on titanium have been used in connecting rods, valves, pistons, etc. Adding 12% TiC to strengthen can reduce weight by up to 44%.
- Forecast of Titanium Market for Automobile in China
Titanium for automobile in China has a broad market. Firstly, China’s economy still has some room for development. The increase of per capita disposable income and urbanization will promote the stable growth of the automobile industry. It is predicted that China’s car ownership will reach about 200 million by 2020. The production and sales of automobiles will reach 23.74 million to 24.18 million in 2013. It is estimated that in 2014, there will be 23.85 million to 24.29 million vehicles, 11.44 million vehicles imported and 1.03 million vehicles exported, with an increase rate of 8%-10%, and the related parts and components industry will continue.
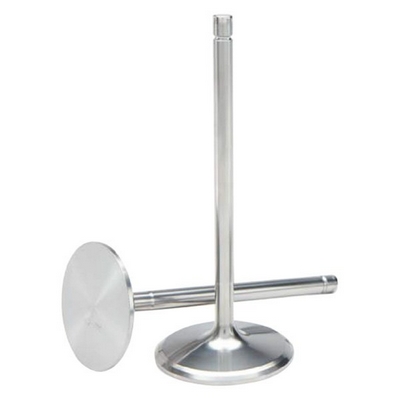
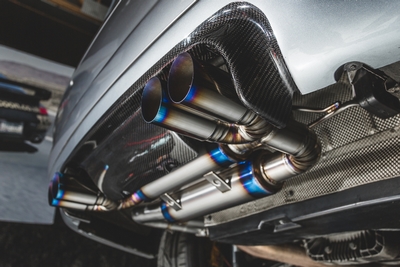